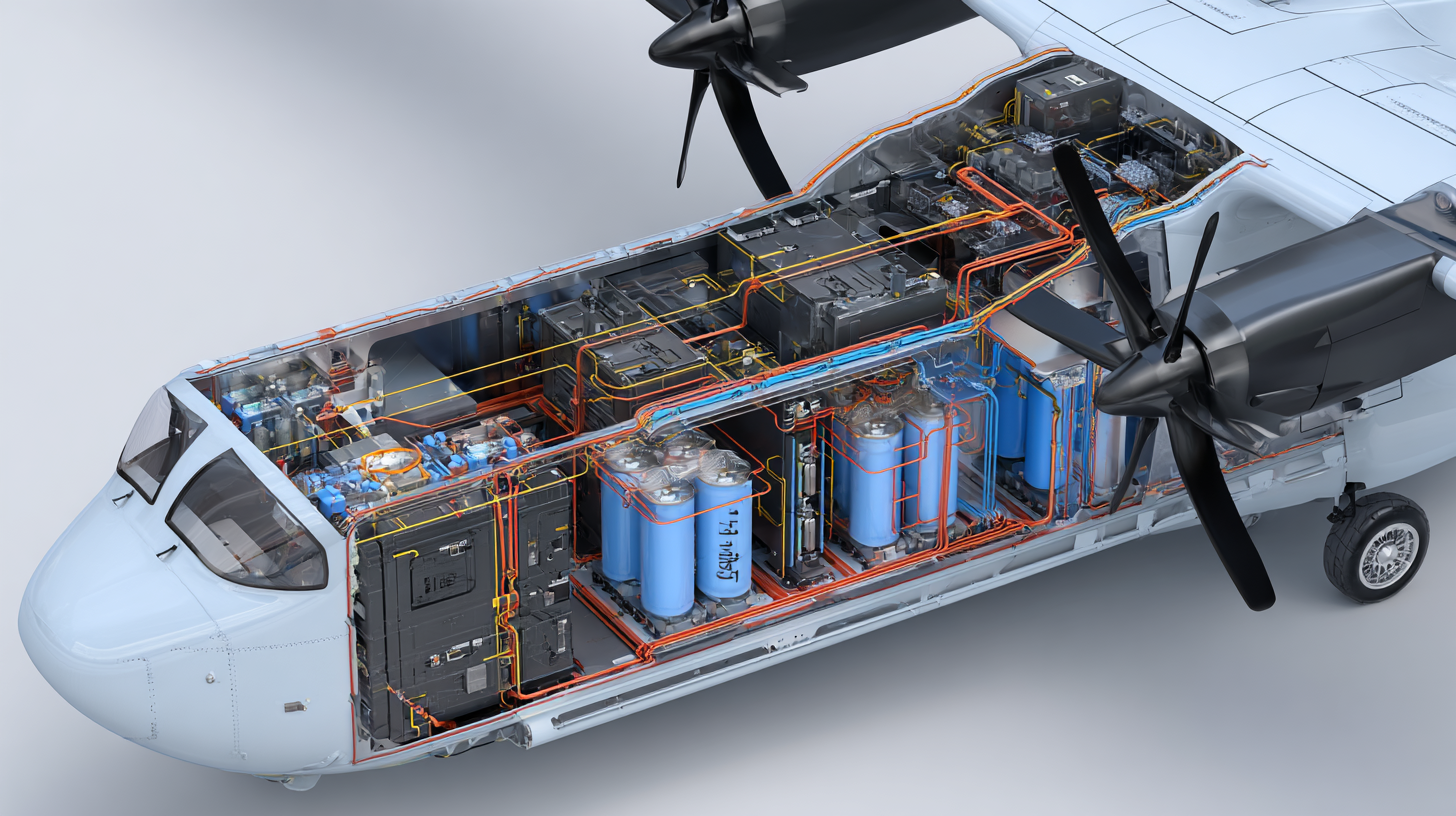
Power Generation Systems for VTOL Aircraft: Powering the Low Altitude Economy
The eVTOL industry has reached a point where commercial viability hinges primarily on power generation systems rather than aerodynamic configurations. Although industry discourse frequently centers on the merits of multirotor versus lift+cruise designs, the true competitive advantage emerges from an aircraft's efficiency in generating, managing, and distributing power across its entire operational spectrum.
Primary power, power conversion, and power distribution components for a more electric aircraft's electrical system
The low-altitude economy—encompassing all commercial activities below 1,000 meters altitude—stands at a critical inflection point, projected to expand from 69 billion in 2023 to over 280 billion globally by 2030. At the heart of this aerial revolution lies a fundamental challenge: power generation and battery technology. As electric vertical takeoff and landing (eVTOL) aircraft emerge as the workhorses of this new economic frontier, their commercial viability hinges entirely on breakthrough energy solutions that balance weight, capacity, and safety.
Recent regulatory developments have accelerated this growth. The FAA's new Special Federal Aviation Regulation for powered-lift aircraft creates the first new civil aircraft category since helicopters in the 1940s, providing a clear certification path for eVTOL operators. This regulatory framework enables companies like Joby Aviation and Archer Aviation to pursue commercial operations in 2025, making power system optimization increasingly critical for market entry.
Infrastructure and Requirements
Vertiport infrastructure development presents significant challenges for power generation and distribution systems. According to comprehensive analysis conducted by the National Renewable Energy Laboratory (NREL), an average vertiport facility requires a minimum charging capacity of 1-megawatt or greater—an energy demand equivalent to powering approximately 800 residential homes simultaneously.
A busy vertiport could consume over 5 megawatts of power, necessitating utility infrastructure upgrades and smart grid technology deployment to manage peak demands. This substantial electrical requirement creates considerable strain on existing power grids and distribution networks. Most urban and suburban electrical systems were not designed to accommodate such concentrated power demands in relatively small geographic areas. Consequently, implementing vertiport facilities typically necessitates major grid infrastructure upgrades, including new substations, transmission lines, and distribution equipment.
The integration of renewable energy sources and energy storage systems at vertiports presents opportunities to reduce grid impact while providing sustainable power for operations.
Application-Specific Power Requirements
Cargo Operations
AutoFlight CarryAll Firefighting Version
Heavy-lift aircraft like the AutoFlight CarryAll require power systems capable of 15C discharge rates during takeoff while maintaining 2,000 kg maximum takeoff weight with 400-500 kg payload capacity. These operations demand battery systems prioritizing sustained high-power delivery over passenger comfort features.
Agricultural Applications
Agricultural drones typically utilize 12S lithium-ion systems with 22,000-30,000 mAh capacity to achieve 15-20 minutes flight time while carrying 15-20 liters of liquid payload. These systems must withstand contamination from agricultural chemicals and frequent charging cycles required for continuous field operations.
Emergency Medical Services
Emergency applications demand the highest reliability standards, requiring immediate response capability with minimal pre-flight preparation time. The crucial 15-minute coverage area of an eVTOL significantly exceeds ground ambulance capabilities, making power system reliability directly impact life safety outcomes.
Infrastructure Inspection
Power line inspection operations require precision hovering capabilities and extended flight endurance in electromagnetic field environments. Professional inspection drones must maintain stable flight while carrying high-resolution cameras and thermal imaging equipment. The electromagnetic interference from high-voltage power lines creates significant challenges for motor control systems, requiring enhanced electromagnetic compatibility.
Tourism Applications
Tourism applications require power systems optimized for smooth flight characteristics and extended hover capabilities for photography and observation. eVTOL aircraft benefit from zero-emission characteristics, enabling access to noise-sensitive areas like national parks where traditional helicopters may be restricted. Power systems must support operations in remote locations with limited charging infrastructure.
Battery Technology: The Energy Density Challenge
Current lithium-ion systems deliver approximately 250 Wh/kg at the system level, substantially below the 800 Wh/kg threshold necessary for economically viable long-range operations. This fundamental limitation constrains aircraft design parameters and operational capabilities, creating the industry's most significant technological barrier.
Advanced Battery Chemistry Development
Internal components of a lithium-ion battery versus an all-solid-state battery
Solid-State Batteries
Solid-state technology offers the most promising near-term solution for energy density improvements. EHang's successful flight test using solid-state batteries achieved 48 minutes of continuous operation—a 90% improvement over traditional lithium-ion systems. These cells incorporate metallic lithium anodes and oxide ceramic electrolytes, delivering 480 Wh/kg while operating across temperature ranges from -40°C to 150°C.
NASA's SABERS project has developed sulfur-selenium cells achieving 500 Wh/kg energy density while eliminating flammable liquid electrolytes. This technology enables 30-40% weight reduction through vertical cell stacking architectures and operates at higher temperatures without complex cooling systems.
Lithium-Sulfur Technology
Researchers at Monash University have created lithium-sulfur cells incorporating polyvinylpyrrolidone that overcome traditional charging speed constraints while delivering energy densities near 500 Wh/kg. This advancement uses chemistry inspired by beta-dine to boost charge and discharge rates, making these batteries suitable for aviation applications requiring high power output.
Electric Motor Technologies: Power Density and Efficiency
Power density comparison of electric motor technologies used in eVTOL aircraft development
Electric motor innovation prioritizes maximizing power density while maintaining efficiency during rigorous flight operations. Current eVTOL motors achieve approximately 5 kW/kg power density, more than double the 2.3 kW/kg typical in automotive applications. Lilium has developed motors producing over 100 kW while weighing only 4 kg, establishing a power density benchmark for aviation propulsion.
Axial Flux Motor Advantages
Detailed cutaway view of an axial flux electric motor, showcasing its internal design for electric aircraft propulsion
Axial flux technology represents a fundamental departure from conventional radial flux designs, positioning magnetic flux parallel to the rotation axis for enhanced power density and efficiency. YASA's axial flux motors deliver 8 kW/kg power density while maintaining 95% efficiency.
Evolito's liquid-cooled axial flux motors achieve power densities exceeding 6 kW/kg while operating at 20,000 RPM5. Their D250 motor features stackable configurations providing twice the torque output with only 10% dimensional increase, enabling effective system scaling and redundancy implementation.
The global axial flux motor market is projected to expand at 26.5% CAGR through 2030, reaching $1.76 billion by 2030, with eVTOL aircraft serving as a primary growth driver.
Superconducting Motor Development
3D render of an eVTOL electric motor, showcasing its integrated power electronics and internal components
Superconducting technology represents the cutting edge of power density advancement. RTX is developing 2.5 MW systems for single-aisle aircraft, with current prototypes operating at 260 kW while achieving electrical efficiency exceeding 99%5. These systems offer significant weight reduction critical for commercial aviation, though cryogenic cooling integration remains challenging.
Hybrid-Electric and Fuel Cell Systems
Hybrid-electric propulsion systems overcome distance constraints of fully electric designs while preserving environmental advantages. Honda is developing hybrid eVTOL aircraft with gas turbine generators paired with batteries, targeting 400 km range capability for economically viable inter-city travel.
Hydrogen Fuel Cell Integration
Hydrogen fuel cell technology demonstrates superior energy density compared to conventional battery systems, achieving power densities of approximately 2,900 W/kg with effective energy density of 300 Wh/kg. United Therapeutics achieved the world's first piloted hydrogen VTOL flight in March 2025, utilizing a modified Robinson R44 helicopter powered by proprietary fuel cell systems.
Joby Aviation demonstrated a 523-mile hydrogen-powered flight using liquid hydrogen storage feeding H2FLY-designed fuel cells, with batteries providing supplemental power during high-demand flight phases. This hybrid approach leverages strengths of both energy storage technologies while minimizing individual limitations.
Power Electronics and Distribution Systems
Equipmake electric motor and associated power electronics unit for eVTOL propulsion
Power electronics serve as the essential interface between energy storage and electric motors, converting DC battery power into variable AC output for precise motor control. Contemporary eVTOL inverters achieve 99% efficiency through silicon carbide (SiC) semiconductor technology, delivering superior switching characteristics compared to conventional silicon IGBTs.
High Voltage Distribution Architecture
eVTOL aircraft commonly utilize high-voltage DC distribution systems ranging from 450V to 850V, reducing power losses and decreasing conductor weight. ASE has developed power distribution systems for Eve Air Mobility featuring primary high-voltage and low-voltage distribution networks with built-in DC-DC converters, providing galvanic isolation and comprehensive health monitoring.
Electrical power distribution architecture for a hybrid eVTOL, detailing high voltage propulsion drives and low voltage system loads
The decentralized configuration of eVTOL propulsion systems presents unique power coordination challenges. VerdeGo Aero addresses this through Integrated Distributed Electric Propulsion (IDEP) technology, integrating multiple electric motors with hybrid generators for responsive attitude control and significant redundancy.
Thermal Management: Critical for Commercial Operations
Thermal management constitutes a significant challenge in eVTOL power system design, as high-power electrical components generate substantial waste heat requiring efficient dissipation. NASA's HEATherR initiative addresses thermal issues in megawatt-scale electrified propulsion systems.
A 3D rendering of a complex thermal management system, likely designed for eVTOL battery packs
Contemporary power systems experience approximately 20% energy loss through heat dissipation, necessitating advanced cooling technologies. HEATherR develops power systems with 75% lower thermal losses while implementing localized passive thermal management solutions.
Battery temperature regulation extends beyond component cooling to encompass maintaining optimal performance within narrow temperature ranges. Lithium-ion batteries require active thermal control systems that add weight and complexity while maintaining ideal temperatures across varying flight conditions.
Future Technological Trajectories
Structural battery applications
The integration of advanced technologies is expected to deliver substantial eVTOL power generation improvements within the next decade. Quantum-enhanced design methodologies for structural batteries represent a groundbreaking breakthrough in aerospace engineering, offering the potential for the development of "Mass-less" energy storage systems. These innovative batteries can be directly incorporated into aircraft structural components, effectively eliminating the weight penalty traditionally associated with separate battery systems. By leveraging quantum computational approaches to optimize molecular configurations and electrochemical interfaces, engineers can design multifunctional materials that simultaneously bear mechanical loads while storing and delivering electrical energy. This integration of energy storage functionality into load-bearing structures could dramatically improve aircraft energy efficiency, extend range capabilities, and enable new electric propulsion architectures without compromising structural integrity or safety margins.
Wireless power transmission technology represents a innovative approach to energy delivery, this technology could revolutionize multiple industries by eliminating the need for large, heavy battery systems that currently constrain operational duration and performance. Oak Ridge National Laboratory has made substantial advancements in this field, successfully developing and demonstrating 100 kilowatt wireless charging systems that achieve an impressive 96% efficiency rate.
Wireless power transmission technology
These high-power, high-efficiency systems provide compelling evidence of the technical feasibility for implementing wireless power transmission in demanding applications such as aviation, where weight considerations are paramount. Continuous power delivery could enable extended flight times or new operational capabilities. Laboratory's achievements suggest that wireless power technology has matured sufficiently to warrant serious consideration for integration into next-generation aircraft designs and other advanced transportation systems.
NASA's sulfur-selenium battery technology projects 44.5% reduction in total cost of ownership through improved cycle life and reduced insurance premiums from enhanced safety characteristics. Strategic industry partnerships between aerospace manufacturers and automotive suppliers are accelerating technology transfer while distributing development costs across multiple market segments.
Certification and Safety Considerations
Certification of electric propulsion systems constitutes a crucial pathway toward commercial operations. The FAA has developed a harmonized certification roadmap with international authorities to streamline validation processes while maintaining rigorous safety standards. Substantial differences persist between US and international certification approaches, particularly regarding electric and hybrid propulsion system approval processes.
NASA's power and energy management research emphasizes the essential role of real-time monitoring and control systems. Certification authorities mandate continuous verification that aircraft maintain sufficient power for critical flight maneuvers while ensuring adequate energy reserves for safe mission completion.
Power generation systems represent the fundamental technological foundation enabling commercial eVTOL operations across the expanding low-altitude economy. Success depends on achieving optimal integration of battery chemistry, motor technology, power electronics, and thermal management while meeting stringent aviation safety and reliability requirements.
The industry's progression toward commercial certification and deployment continues, with power system advancement serving as the primary catalyst for urban air mobility transformation. As regulatory frameworks mature and technology costs decrease, the companies that master power generation integration will define the future of advanced air mobility operations.
The path forward requires continued innovation in energy storage density, motor efficiency, and system integration while maintaining the safety standards essential for public acceptance and regulatory approval. The low-altitude economy's $280 billion potential by 2030 depends directly on solving these power generation challenges at commercial scale.